Here are some common applications of grooved welded outlet:
Fire sprinkler systems
Grooved welded outlets are commonly used where sprinkler pipes connect to overhead piping systems in commercial buildings. The grooved connection provides a fast and reliable sealed joint.
Industrial piping systems
In factories and industrial facilities, grooved welded outlets may be used to connect different pipe runs together or to connect pipes to equipment like machines, pumps, valves, etc. Their reliability makes them suitable for critical process piping.
Sea water systems
On ships and offshore structures, grooved welded outlets are frequently used in sea water piping systems that provide cooling, fire protection or other water needs. They hold up well against corrosion from salt water.
HVAC systems
Heating, ventilation and air conditioning systems in large commercial buildings often utilize grooved welded outlets to connect different parts of the piping network together with flexible and secure joints.
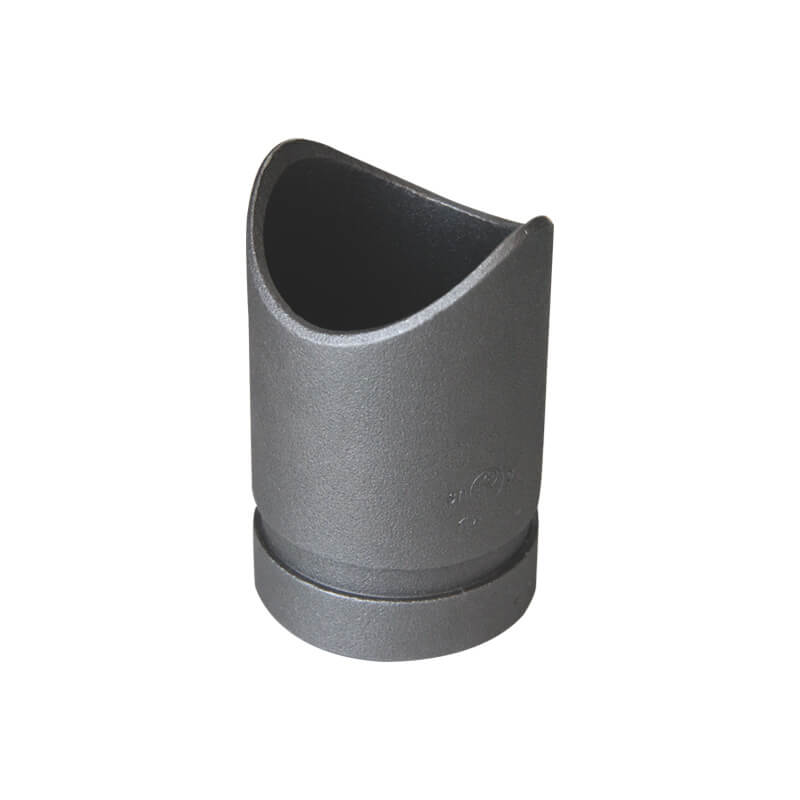
District heating/cooling systems
Central piping that distributes heated or cooled water/fluid around a campus, community or municipality may incorporate grooved welded outlets at connection points to buildings or other infrastructure.
Oil/gas pipelines
Grooved welded outlets help construct reliable joints in pipelines that transport oil, natural gas or other fuels over long distances.
Their strength, flexibility and secure seal make grooved welded outlets a common choice for industrial, commercial and infrastructure piping applications where leak-proof joints are critical.